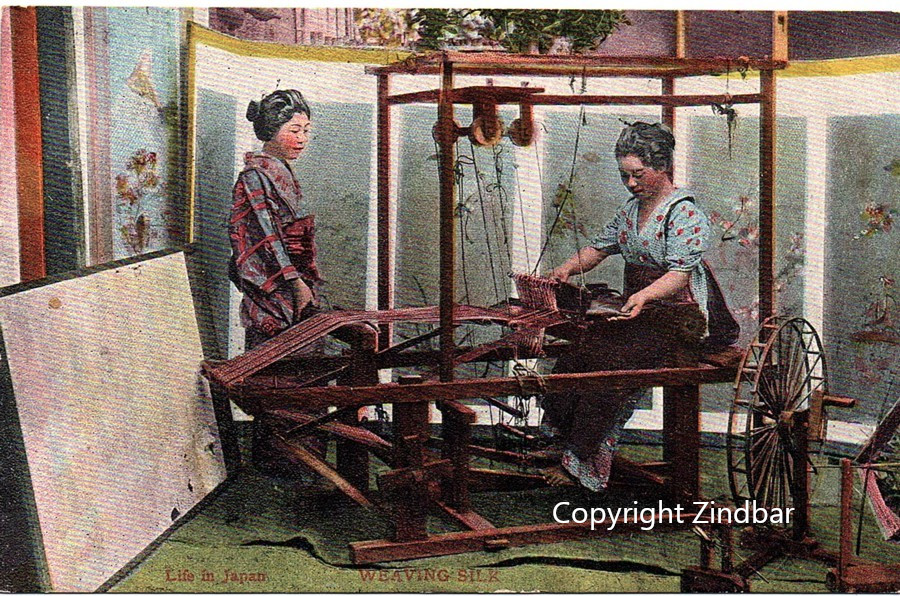
While China has for centuries been known for its production of silk since 5000 to 3000 before the Common Era, silk manufactured in Japan began in the 4th century eventually led this island nation in Asia to adopt the technology required to improve silk weaving. In turn, these methods led to the modernization and industrialization of Japan, which led it to being the number one producer of silk at the start of the twentieth century.
The history of silk weaving in Japan started when the Empress Iwa-no-Himo became intrigued by the silkworm which could spin fine threads into a luxurious fabric, according to an article in The Manchester Guardian, London, England dated August 24, 1891. Arriving in Japan by the way of Korea from China, silk as a fabric proved to be useful in the creation of traditional Japanese garments for everyday use as well as ceremonial use. Even special brocaded silks were woven especially for clothing worn by the Japanese emperor and empress and other dignitaries. Likewise, silks also made up the many costumes worn by Japanese theatre actors in Kabuki and Noh performances. These silks often had threads of silver and gold woven into the fabric design, creating a rich, elegant look. Silk was also imported from Japan to Europe in the 12th century as part of the then-known world global trade.
For centuries the production of silk in Japan has been done without having to export any of the raw materials required to make silk, including the mulberry farms which attract the silkworm, scientifically known as Bombyx mori. Sericulture, or silk farming, originates from the silkworm’s cocoon. The cocoon must be unraveled before it can be boiled, then wound on large spools, often being twisted with other silk strands to form one continuous thread. This large spool is then dipped into a vat of dye, dried, then transferred to still smaller spools which could be worked from more easily. The last procedure is refining the silk thread before it is wound onto wood bobbins, which are then ready to be woven into silk fabric. Since the silk weaving factories purchase raw silk, they often had to process silk threads from start to finish before it becomes the final product for use in weaving fabric. Both physical labor and machine reelers were used to gather the raw silk during the farming process.
The loom used in Japan for weaving silk was made of wood, and the pedals of the Japanese silk loom were operated by the weaver, who pressed the pedal with their foot about once every second in a minute’s time. Due to the nature of the machine, only fifteen feet of silk on average was woven on this loom each day. Between eight to thirteen silk fibers were spun together to create a single thread of silk during the manufacturing process. Silk threads were also used in the art form of Kumihimo, or silk braiding, often used for decoration in garments as well as simple ties at the waist on men’s kimonos, Samurai armor and swords, and interior décor. Special wood looms were designed just for braiding Kumihimo.
In the mid-1800’s, the French Jacquard loom was introduced in Japan. This innovative fabric weaving loom became a precursor to the early computer used during the mid-nineteenth century, using a series of punched cards to “program” the design into the fabric. Discovering that the Jacquard loom could create elaborate designs in the silk fabric, the Japanese learned to create some of the world’s most beautiful damask and brocade silks, quickly becoming the highest quality of silk produced in Asia at the time. According to an article in Minneapolis Daily Times dated May 23, 1895, it was not uncommon for a silk weaving factory to have numerous looms all working at the same time, often with the wooden boards clapping loudly against each other, the silk threads forming the fabric to be made into garments.
Regular looms which do not weave an elaborate design into the fabric like a Jacquard loom were often located in individual private homes. Plain, solid colored woven silk was always a welcome product which could then be sewn into many a kimono for the family or even as contract work for a larger silk weaving company in Japan.
A large variety of silk fabric was produced in Japan. Habutae silk, manufactured in Kyoto, was often simple, lightweight, and ivory in color, undyed silk which could be used in undergarments or shirts. Kaiki silk was also lightweight but usually dyed bright colors used in kimonos for children and young ladies. Fuji silk was another lightweight silk with a natural luster to it. Shantung silk is often used in formal attire like suits and women’s jackets, with its threads often irregular in appearance, commonly known as ribs, or ribbed silk. Other varieties of silk include georgette crepe, flat crepe, and organdy. The Suzuri method of weaving in silk is primarily used in the creation of wall hangings used in Japanese homes. Due to the high quality of silk manufactured in Japan, much of it was imported by the western world during late nineteenth century.
While many nations in the western world now produce their own silk, Japanese silk, especially antique silk, is usually purchased and collected for its quality and design.
Image Credit: Zindbar